Trends in Fineblanking Technology Examples of Applications in Transmission Systems
Fineblanking คือกระบวนการการขึ้นรูปโลหะที่มีเอกลักษณ์เฉพาะตัวของเครื่องจักรและแม่พิมพ์ เป็นกระบวนการผสมผสานระหว่างการปั๊มและการขึ้นรูปเย็น (Cold Extrusion) ซึ่งสามารถลดขั้นตอนการแต่งผิวที่ทำให้ชิ้นงานสมบูรณ์กว่าการปั๊มแบบทั่วไป (normal press) ชิ้นงานจากกระบวนการ Fineblanking จะมี clearance น้อยกว่ากระบวนการปั๊มอื่นๆ ทำให้ขอบเรียบตรง รวมถึงการทำรูเล็กๆและขอบบางๆที่สัมพันธ์กับความหนาของโลหะ ชิ้นงานมีความเรียบสูง (Flatness) นอกจากนี้ยังให้ปริมาณผลิตสูงด้วย (High Volume Production) ความแตกต่างระหว่างชิ้นแรกและชิ้นสุดท้ายที่ผลิตมีน้อยมาก
เปรียบเทียบความแตกต่างระหว่างการปั๊มขึ้นรูปแบบเดิม (Conventional blanking) และการขึ้นรูปแบบ Fine Blanking
ชิ้นงานที่ผลิตจากการปั๊มขึ้นรูปแบบธรรมดาจะถูกกดด้วยแรงเพียงแรงเดียวคือแรงกดตัด (Punch force) ซึ่งจะเฉือนผิวหน้าที่ตัดอย่างแรงและผิวจะไม่เรียบ นอกจากนั้นแล้วการขึ้นรูปด้วยแม่พิมพ์ที่มีค่า clearance สูง จะไม่ได้ขนาดและมุมของชิ้นงานที่ถูกต้อง และผิวหน้ารอยตัดจะหยาบ ต้องนำไปผ่านขั้นตอนการผลิตและตกแต่งผิวอื่นๆอีก
ส่วนชิ้นงานจาก Fineblanking นั้นเกิดจากการปั๊มขึ้นรูปด้วยแรงสามแรงที่กระทำโดยให้ค่า clearance ที่น้อยที่สุด ให้ผิวหน้าและมุมของชิ้นงานที่สวยงาม แม่นยำ ไม่เกิดรอยแตก และยังทำให้ผิวงานเรียบที่สุด จึงไม่ต้องนำชิ้นงานไปผ่านขั้นตอนอื่นๆอีก
การนำเทคโนโลยี Fineblanking มาใช้ร่วมกับกระบวนการอื่นๆ ได้ทำให้เกิดนัยสำคัญด้านการลดต้นทุนทั้งตัววัสดุและลดค่าใช้จ่ายในการผลิต Feintool ซึ่งเป็นบริษัทผู้ผลิตระบบงานตัดขึ้นรูปแบบละเอียดระดับโลกจากประเทศสวิสเซอร์แลนด์ มีประสบการณ์ด้านการผลิตด้วยกรรมวิธี Fineblanking กับลูกค้าซึ่งเป็นผู้ประกอบการชั้นนำในอุตสาหกรรมยานยนต์ของโลก โดยได้มีส่วนเกี่ยวข้องและร่วมทำงานกับลูกค้าตั้งแต่ขั้นต้นเพื่อให้มั่นใจว่ารายละเอียดในการออกแบบสามารถสอดรับกันได้อย่างพอดีกับการผลิต ไม่อย่างนั้นแล้วกระบวนการย้อนกลับทางวิศวกรรมหรือที่เรียกว่า re(verse) engineering จะมีความจำเป็นในขั้นท้ายของวงจรการผลิต ซึ่ง MEN Thailand เห็นตัวอย่างการทำงานร่วมกันกับลูกค้าในการช่วยพัฒนาประสิทธิภาพด้านการผลิตเป็นเรื่องราวที่น่าสนใจเรียนรู้
ระบบงานตัดขึ้นรูปแบบละเอียดหรือ Fineblanking คือเทคนิคอันทรงประสิทธิภาพสำหรับกระบวนการขึ้นรูปชิ้นส่วนสำเร็จความละเอียดสูงที่ใช้ประกอบเป็นผลิตภัณฑ์ ทั้งนี้ขึ้นอยู่กับผู้ผลิตแต่โดยทั่วไปแล้วในรถยนต์สมัยใหม่คันหนึ่งๆ จะประกอบด้วยชิ้นส่วนที่ผลิตด้วยวิธี Fineblanking ระหว่าง 50-200 ชิ้น ซึ่งโดยมากเป็นการนำไปใช้ในงานแอพลิเคชั่นหลักๆ ที่ผู้บริโภคมองไม่เห็น ตัวอย่างเช่น ระบบล็อค กลไกสำหรับอุปกรณ์ปรับเบาะนั่ง ชิ้นส่วนต่างๆ ในแอร์คอมเพรสเซอร์ ถุงลมนิรภัยและระบบเข็มขัดนิรภัย รวมถึงชิ้นส่วนต่างๆ ในระบบส่งกำลังของเครื่องยนต์ซึ่งต้องใช้ชิ้นส่วนที่มีความละเอียดสูงเช่นกัน อาทิ ตั้งแต่ท่อในระบบการปล่อยไอเสีย ไปจนถึงการใช้งานต่างๆ ในระบบชุดเกียร์ทั้งแบบออโต้และแมนนวล รวมถึงคลัชท์และคอนเวิร์ทเตอร์
เมื่อไม่กี่ปีที่ผ่านมานี้มีความเป็นไปได้ต่างๆ เกิดขึ้นอย่างมากมาย การผสมผสานของกระบวนการผลิตต่างๆ เพื่อเป็นตัวช่วยให้การออกแบบชิ้นงานมีความหลากหลายมากขึ้น เพื่อให้เห็นภาพที่ชัดเจนขึ้น มีสองตัวอย่างชิ้นงานในระบบ power train ของรถยนต์ที่ได้แสดงให้เห็นถึงการจัดวางกลยุทธ์ของกระบวนการผลิตในปัจจุบัน
ตัวอย่างที่ 1 : แผ่นส่งกำลังระบบเกียร์
รถยนต์ขนาดเล็กรุ่น “Smart” ที่เป็นที่นิยมในยุโรปนั้น ในขั้นตอนของการทำต้นแบบ เดิมทีได้มีการออกแบบแผ่นส่งกำลังระบบเกียร์ (Drive plate) ซึ่งเป็นส่วนหนึ่งของชุดขับเคลื่อนโดยการผลิตด้วยแมชชีนนิ่ง แต่จากผลของโครงการลดต้นทุนการผลิต ทำให้มีการออกแบบชิ้นส่วนนี้ใหม่ภายใต้ความร่วมมืออย่างใกล้ชิดโดยคณะผู้เชี่ยวชาญจากแผนกวิศวกรรมของ Feintool เพื่อให้การออกแบบชิ้นส่วนมีทิศทางเดียวกับแนวคิดที่ได้ออกแบบไว้ตั้งแต่แรก โดยคงรักษาฟังก์ชั่นใช้งาน แต่สามารถลดน้ำหนักลงจากการลดการใช้วัสดุ
การลดน้ำหนักไม่จำเป็นต้องหมายความว่าใช้วัสดุที่มีน้ำหนักเบากว่าเสมอไป หลายๆ ส่วนไม่สามารถลดน้ำหนักลงได้อีกเนื่องจากจำเป็นต้องคำนึงถึงความสามารถในการรับน้ำหนักด้วย ดังนั้น การใช้วัสดุที่มีน้ำหนักเบากว่าเช่นอลูมิเนียมจึงมักจะไม่ใช่แนวทางในการแก้ปัญหาที่ดี เนื่องจากจำเป็นต้องเพิ่มความหนาเพื่อให้มีความแข็งแรงตามที่ต้องการ
Feintool แก้ปัญหานี้โดยการลดปริมาณวัสดุ เช่น ใช้วัสดุที่บางกว่า แต่มีความแข็งแรงต่อน้ำหนักมากขึ้น ซึ่งวัสดุประเภทนี้ได้ปรากฏให้เห็นตามท้องตลาดบ้างแล้ว และบรรดาผู้พัฒนาวัสดุประเภทโลหะต่างก็กำลังเร่งดำเนินการพัฒนาไปในทิศทางนี้แล้ว เช่น fine grain steel หรือ multi-phase steel เป็นต้น
สำหรับความท้าทายที่มีต่อภาคการผลิตก็คือ การพัฒนาเครื่องมือเครื่องจักรที่ใช้ในการผลิตเหล็กกล้าเหล่านี้ ซึ่งในที่นี้หมายถึงเทคโนโลยี fineblanking และเทคโนโลยีการขึ้นรูป ประสิทธิภาพของกระบวนการผลิตชิ้นส่วนก็เป็นส่วนหนึ่งที่ช่วยให้สามารถลดน้ำหนักลงเป็นจำนวนมาก
วิธีการที่กล่าวมานี้สามารถลดน้ำหนักลงได้ถึง 70% โดยใช้เทคโนโลยี Fineblanking ร่วมกับการพัฒนารูปทรง และยังสามารถลดหมุดยึดตำแหน่งลงได้อีกสองตัว โดยนำหมุดแบบ preblanked (semi-pierced) มาใช้แทน
ตัวอย่างที่ 2 : แป้นคันเกียร์
ช่วงก่อนที่จะมีการปรับโครงสร้างรูปแบบทางวิศวกรรม (Reverse engineering) แต่เดิมนั้นแป้นคันเกียร์จะมีสลักอยู่ที่ปลายแต่ละด้านและไม่ใช่รูปแบบที่มีความมั่นคงนัก
ดังนั้น ลูกค้า ผู้ผลิตชิ้นส่วน และกลุ่มผู้เชี่ยวชาญของ Feintool ได้ร่วมมือกันคิดค้นวิธีการและรูปแบบที่เหมาะสมเพื่อนำมาหลอมรวมเป็นแนวทางในการแก้ปัญหานี้ ซึ่งแนวคิดเหล่านี้ได้ถูกประเมินและจัดอันดับโดยใช้ FMEA ในการออกแบบและผลิตเครื่องมือ หลังจากทำต้นแบบละเอียดแล้ว ได้มีการพัฒนาและปรับปรุงอีกครั้งหนึ่ง ผลลัพธ์ที่ได้ประกอบด้วยส่วนประกอบสี่ส่วนที่อยู่บนแป้น ซึ่งนำมาเชื่อมติดกันด้วยเลเซอร์ เครื่องมือชุดใหม่นี้ถูกออกแบบมาเพื่อทำหน้าที่แทนแป้นและส่วนประกอบเล็กๆ อีกสามชิ้น
จากแนวความคิดเดิมซึ่งมีการผลิตทั้งสิ้น 17 ขั้นตอน และมีข้อผิดพลาดที่สำคัญหลายประการ เช่น การเสียรูปจากการบิด การคืนตัว และการเสียรูปจากแรงกระทำ สายการผลิตใหม่ที่ถูกพัฒนาขึ้นมา มีเพียง 10 ขั้นตอน มีความผิดพลาดน้อยกว่าและใช้วัสดุน้อยกว่า นอกจากนี้ ยังสามารถลดระยะเวลาในการผลิตลง 40 เปอร์เซ็นต์ และลดต้นทุนการผลิตลงถึง 50 เปอร์เซ็นต์
สรุป
Fineblanking เป็นกระบวนการสำคัญในการผลิตระบบส่งกำลัง และในปัจจุบันเราสามารถพบเห็นชิ้นส่วนที่ผลิตด้วยวิธีการนี้ในทุกๆ ส่วนของระบบส่งกำลัง รวมทั้งส่วนประกอบอื่นๆของรถยนต์ กระบวนการนี้มีบทบาทสำคัญในการลดต้นทุนการผลิตและลดปริมาณวัสดุที่ใช้ โดยเฉพาะอย่างยิ่ง การนำ Fineblanking มาใช้ร่วมกับเทคนิคการขึ้นรูปแบบอื่นๆ จะทำให้เกิดวิธีการผลิตที่น่าทึ่งที่ช่วยให้ระบบต่างๆ สามารถทำงานได้อย่างเต็มประสิทธิภาพ
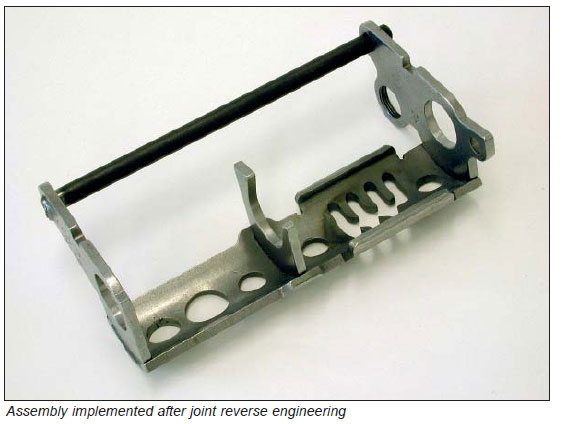

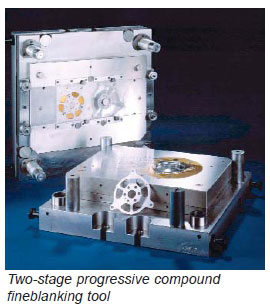

Fineblanking, as a process, has three motions and specially designed tooling. The combination of the fineblanking press with fineblanking tooling creates parts with fineblanking’s hallmark fully sheared, straight cut edges. It also produces parts with small holes and thin web sections relative to material thickness, parts with excellent flatness, and parts that have very little dimensional variation from the first part through the millionth part ¬ and beyond.
In short, fineblanking is an extremely precise high volume manufacturing process. Depending on the functional and cosmetic requirements of any given metal component.
Fineblanking presses come in a wide range of sizes. The smallest is 160 tons and the largest commercially available is 1400 tons.
Comparison of the conventional blanking and fineblanking processes
Parts produced by normal blanking on a press with only one punch force display severe chipping of the cutting surface and are not flat. Cutting surfaces produced in tools with a large cutting clearance are not at right angles, have a very rough surface and cannot be used without follow-up machining operations.
Fineblanked parts which are produced on a press with three active forces and in tools with minimal cutting clearance have clean, right-angled cutting surfaces with no torn or chipped edges and are extremely flat. This enables them to be used without any need for reworking.
Fineblanking is an efficient technique for the production of precision sheet-metal parts ready for assembly. Depending on the manufacturer, between 50 and 200 fineblanked parts, for instance, are installed in a modern car. The main application areas are “invisible” for the end consumer, for example lock systems, seat adjuster mechanisms, components for air conditioning compressors, airbag and seat belt systems. They also include applications in the entire power train, from the individual tab in the control chain to the exhaust flange, plus many different applications in manual and automatic gearboxes, clutches and converters.
Over the past few years, the range of possibilities has grown considerably: combinations with associated processes are continually adding new dimensions to component design. Two typical examples from power train technology impressively demonstrate the potential of the process as deployed today.
Example: Drive plate
The drive plate forms part of the drive unit of the first “Smart” car and, in the prototype phase, was originally planned as a machined component. As a result of cost-cutting programmes this part was reengineered in close cooperation with the experts in the Feintool Engineering department, retaining the installation dimensions of the original design.
Weight saving does not necessarily mean using lighter materials. In many areas this is not possible because the component has to meet requirements in terms of loadability. Also, it frequently makes no sense to use lighter materials such as aluminium if they then have to be thicker in order to achieve the required strength.
The approach taken by Feintool is aimed at using less (i.e. thinner) materials, but ones of proportionately higher strength. Materials of this type are already available on the market and the steel developers have already set the trend in this direction in motion (fine grain steels, multi-phase steels, etc.)
The challenge on the production side is now to develop tool systems with which these steels can be processed, which in these cases means fineblanking and forming. Large weight savings can be made additionally by optimizing the component for the production process.
The solution described brought about a weight saving of some 70% by using the fineblanking/forming variant, and two positioning pins could also be dispensed with. This function is now performed by preblanked (semi-pierced) pegs.
Example: Gear shift gate
Before reverse engineering, the gear shift gate was designed with two bent-up lugs at either end, but could not be produced reliably in this form.
So the end customer, the designated manufacturer of the part and the Feintool specialists got together in an expert group and came up with a wealth of individual solution ideas in a workshop, which were then distilled into solution concepts. These concepts were evaluated and prioritized using FMEA design and production tools. After detailed prototyping this solution was developed and implemented. The solution consists of a total of four individual components which are positioned on gauges and then welded by laser. A progressive compound tool was designed for producing the actual gate and a compound tool for the three small parts.
From an original concept with 17 production steps and with several potential sources of faults (bending distortion, springback, hardening distortion) a process chain consisting of only ten individual operations, fewer fault sources and lower material consumption has been developed. All in all, a verifiable reduction in throughput time of 40% and a 50% reduction in production costs have been achieved.
Conclusion
Fineblanking is a key process in transmission system production applications. Fineblanked components can be found today in virtually all types of power transmission. The method plays a role in cutting the costs of production and reducing the amount of material used in such systems. In particular, the combination of fineblanking with other forming techniques results in some interesting solutions with maximum concentration of functions.